Tin whiskers are electrically conductive, single crystal eruptions that can grow from surfaces where tin is deposited on a substrate surface (Fig. 1). High aspect ratio Sn whiskers are typically 1-5 µm in diameter and between 1-500 µm in length. They present reliability problems for the electronics industry with ongoing reports of tin whisker induced failures, particularly in the satellite and defense sectors (Fig. 2). Further, the current worldwide initiative to reduce the use of lead (Pb) is driving the electronics industry to consider high tin alternatives to the widely used Sn-37Pb alloys used for plating and solder. Continuing reports of tin whisker induced failures coupled with the lack of an industry-accepted understanding of tin whisker growth and/or test methods to identify whisker-prone products has made blanket acceptance of pure tin plating a risky proposition for high reliability systems. Harsh environments may exacerbate the problem by causing thermal and/or mechanical stresses in tin coated surfaces, leading to the growth of tin whiskers and to tin whisker induced failures. A common failure mode for whisker-prone electronic systems is whisker bridging, which causes electrical shorts (Fig. 3-4).
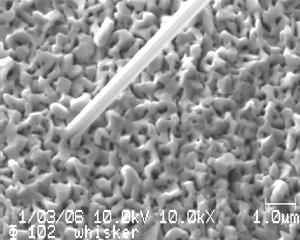 |
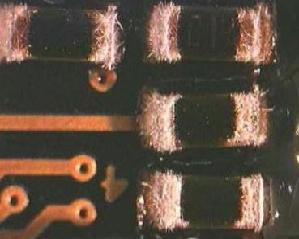 |
|
Figure 1: Typical Sn whisker on a Pb-free connector pin. |
Figure 2: A forest of Sn whiskers on chip resistors (Courtesy N. Asrar, “Tin Whisker Formation on Electronic Product,” ASM International, 20 June 2007). |
|
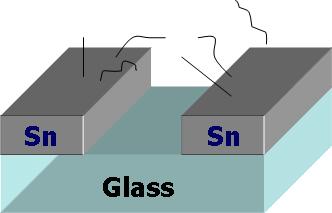 |
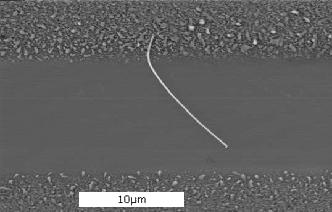 |
|
Figure 3: CAVE test structure to employed to observe Sn whisker bridging failures. |
Figure 4: SEM micrograph showing near-briding Sn whisker after 3 months of incubation in a Sn-on-glass system. |
|
In addition to applied studies of whisker mitigation work on field parts, CAVE is currently conducting experiments to elucidate the fundamental mechanisms of whisker growth. This work is needed to develop a detailed understanding of the physical mechanisms leading to initiation and growth of tin whiskers and to reduce whiskering in Pb-free electronic components. While tin whisker growth is believed to be largely mechanical, there is currently no general agreement on the mechanism governing the growth of tin whiskers.
Previous investigations on whiskering have been hampered by lack of a reproducible means of growing laboratory controlled Sn whiskers in a reasonable time frame. Whiskers often display a long (months and years) and unpredictable incubation period before significant growth occurs. A technological advance has been the ability to consistently grow whiskers in a reasonably short period of time by using sputtered thin films grown under a variety of controlled intrinsic film stress conditions. By using controlled amounts of background Ar gas during the sputtering process, we have been able to achieve films with varying degrees of compressive stress to aid in reproducible whisker production. In addition, sputtered films avoid the complications of electrodeposited films and, in addition, allow us to grow very thin films (~ 0.1 micrometer), which has enabled several key advances involving whisker growth.
Currently, we are investigating the role of calibrated, controlled humidity on whisker production and the role of electric fields in the whiskering process. Humidity is important due to the preponderance of studies which report enhanced whisker growth in the presence of oxygen. Further, in the cracked oxide theory of whisker growth, sufficient compressive stress is presumed to occur at positions of oxide weakness which are the locations of whisker emission. A unique viewpoint of the whisker surface oxide is afforded by in-situ, real-time scanning electron microscopy (SEM) observations of Sn whiskers during heating to temperatures greater than the melting point of Sn. As the Sn melts, the whiskers buckle, curl, and drain of liquid Sn, leaving behind a thin, solid, emptied tube of tin oxide with its higher melting point. With further electron-beam heating, the tin oxide tube frequently forms a coagulated spherical ball of material which is the final resting place of the dead whisker skeleton.
|
Representative Recent Publications
Z. Wang, G. T. Flowers, M. Bozack, The Influence of Limitation of Sputtered Tin Area Through Mesh Grids on Sn Whiskering, 2020 IEEE 66th Holm Conference on Electrical Contacts and Intensive Course (HLM), 2020, pp. 137-143.
R. L. Jackson and E. R. Crandall, The Effect of Convection on Electro-thermal Modeling of Whisker Shorting, 2019 IEEE Holm Conference on Electrical Contacts, 2019, pp. 262-269.
R. L. Jackson and E. R. Crandall, A Multiphysics Coupled Electro-thermo-mechanical Model of Whisker Shorting, 2018 IEEE Holm Conference on Electrical Contacts, 2018, pp. 48-55.
E. R. Crandall, F. Schabert, H. Schmidt, M. Blecher, T. Fili, W.E. Mueller-von Fischer, C. Borhauer, S. Thoss, J. Villarreal, B. Kerckhoff, New LITESURF plating for the mitigation of whisker risks in press-fit applications, 2017 IEEE Holm Conference on Electrical Contacts, 2017, pp. 132-138.
|